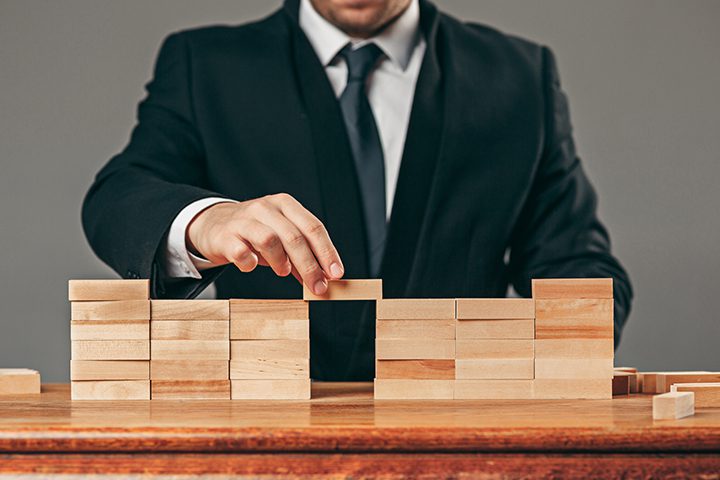
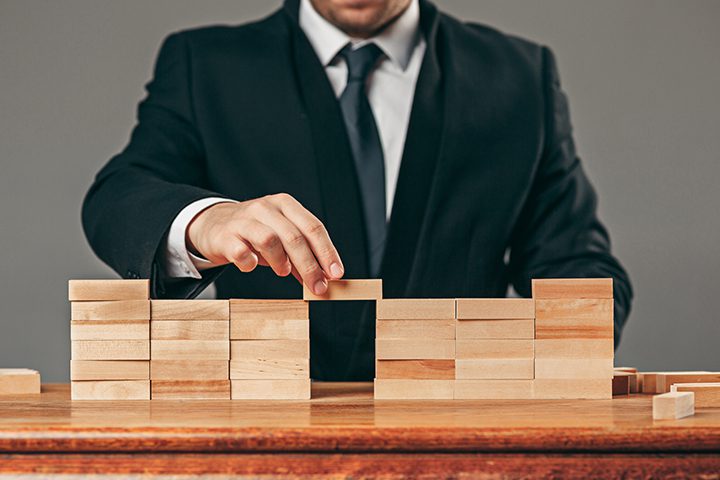
In this post, we will show you some relevant points about ISO 9000 for you to learn once and for all. So, let’s see! In practice: ISO 9000 – International Organization for Standardization is a generic name given to a series of standards that were created for the Quality Management Systems (QMS) sector within a company, which shows its ability to meet the desires of its customers.
ISO 9000 is divided into three parts.
First of all, know that its value becomes great. Because it is compatible with other management systems:
- ISO 9000:2005 – Fundamentals and vocabulary;
- ISO 9001:2008 – Requirements;
- ISO 9004:2010 – Guide to performance improvement.
ISO 9000 certifies that the company is doing processes correctly, but does not guarantee the quality of the final product, and therefore, the need for continuous improvement is strongly encouraged.
This framework focuses on the four main areas of business: resource management, product quality, maintenance of quality records, and the requirement for continuous improvement. It is relevant to all types of companies, products, and services. Therefore, it does not have specific relevance to the IT area.
However, if there is a quality problem in the system, the company will have a loss in production and waste of resources. Thus, the implementation of this system may reduce this loss.
ISO 9000: Quality Management Principles
The set of ISO 9000 standards was developed based on eight quality management principles, with a process-oriented structure.
These principles end up being the main fear of any company since they validate how they affect quality. They reflect the best market practices, since they are designed to allow continuous improvement of the business and capable of responding to the desires and aspirations of customers.
When reading the next 8 PRINCIPLES, see which ones, when used for an IT area, become milder:
- Customer focus: the company must surprise customers in delivering products and services;
- Leadership: leadership is not tyranny, it is organization;
- People involvement: unity brings individual skills as a benefit;
- Process approach: full knowledge of the process, making real problems solved;
- Systematic approach to management: all processes are interrelated;
- Continuous Improvement: continuous improvement seeks to satisfy customers and all parties attracted, through measurement and analysis of results that add value to the company;
- Factual approach to decision-making: decisions made through measurement and analysis of results become effective;
- Mutual benefits in supplier relationships: partnerships must be made so that all parties involved benefit.
It seems obvious that companies do not want to deliver poor services, but sometimes the fact that the company obtains the ISO 9000 standard intensifies the problems. This happens because now processes and indicators are being monitored and evidenced. Apparently, it should not be bad for the company since it creates a good chance for improvement.